Sie haben eine Herausforderung in der Produktionstechnik?
Ob Prozessanalyse, virtuelle Inbetriebnahme oder Industrial IoT – wir entwickeln gemeinsam mit Ihnen praxisnahe Lösungen für Ihre individuellen Fragestellungen. Sprechen Sie uns gerne an!
Unsere Fachbreiche
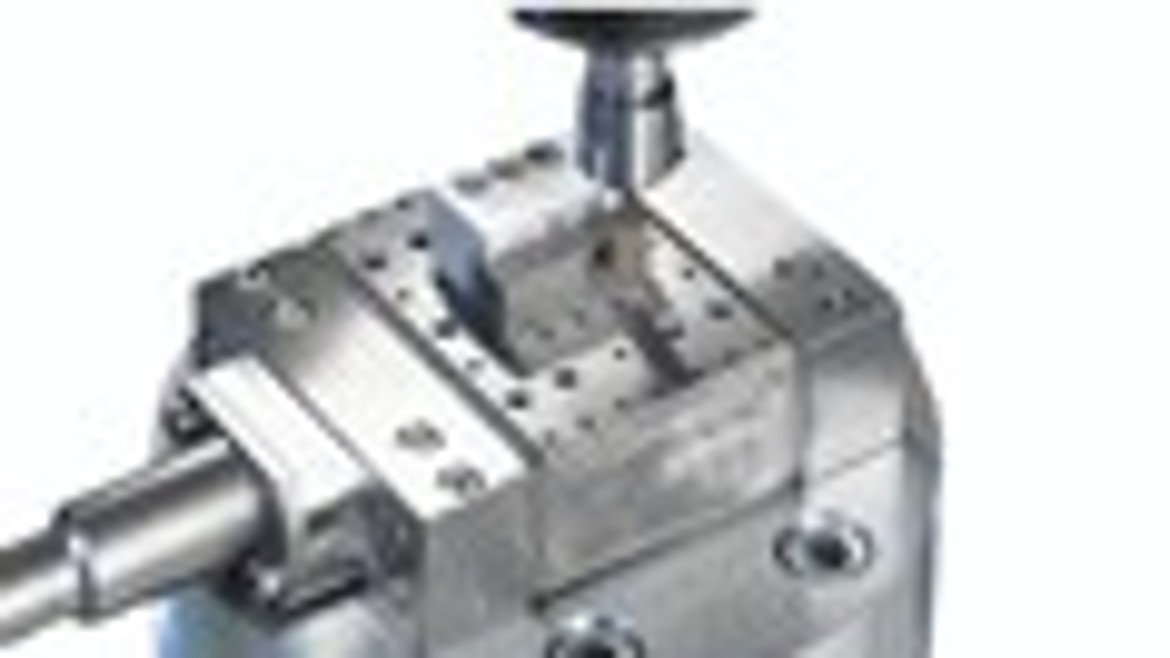
Zerspanungskraftmessungen werden durchgeführt, um die während des Zerspanungsprozesses wirkenden Kräfte zu erfassen und zu analysieren. Die gewonnenen Daten sind entscheidend für verschiedene Aspekte der Fertigungstechnik:
- Werkzeug- und Prozessoptimierung – Durch das Messen der Zerspankräfte kann die Werkzeuggeometrie, Schneidstoffwahl und Prozessparameter (z. B. Vorschub, Schnittgeschwindigkeit) optimiert werden, um Verschleiß zu minimieren und die Standzeit zu erhöhen.
- Maschinen- und Werkstückbelastung – Die Messung hilft, die Belastung auf die Maschine und das Werkstück zu bestimmen, um mögliche Deformationen oder Schäden zu vermeiden.
- Prozessüberwachung und Qualitätssicherung – Abweichungen in den Zerspankräften können auf Werkzeugverschleiß oder Prozessinstabilitäten hinweisen. Die Messung ermöglicht eine frühzeitige Fehlererkennung und damit eine höhere Fertigungsqualität und Prozessrobustheit.
- Materialcharakterisierung – Unterschiedliche Werkstoffe erzeugen unterschiedliche Zerspankräfte. Die Messung hilft, das Zerspanungsverhalten neuer Materialien besser zu verstehen und geeignete Bearbeitungsstrategien zu entwickeln.
- Reduzierung von Energieverbrauch und Kosten – Optimierte Zerspanungsprozesse reduzieren den Energieaufwand und minimieren den Materialverschleiß, was die Produktionskosten senkt.
Zerspanungskraftmessungen liefern essenzielle Daten für eine effiziente, wirtschaftliche und qualitativ hochwertige Zerspanung.
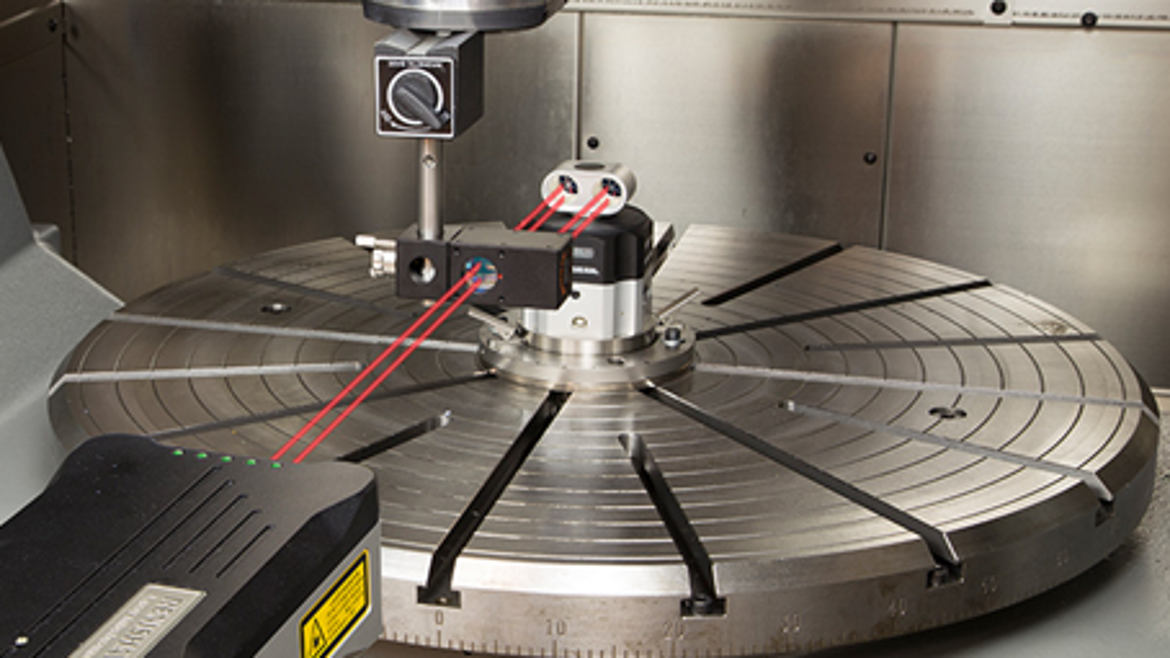
Werkzeugmaschinenvermessungen werden durchgeführt, um die Genauigkeit, Leistungsfähigkeit und Qualität einer Maschine sicherzustellen. Die Hauptziele sind:
- Überprüfung der Maschinengeometrie – Kontrolle von Geradheit, Rechtwinkligkeit, Parallelität und Ebenheit der Achsen und Führungen.
- Erhöhung der Bearbeitungsgenauigkeit – Reduzierung von Fertigungsfehlern durch Korrektur von Abweichungen.
- Kalibrierung und Justierung – Anpassung der Maschine an vorgegebene Toleranzen und Standards.
- Fehlersuche und -diagnose – Identifikation von mechanischen oder thermischen Einflüssen, die sich negativ auf die Präzision auswirken.
- Überwachung des Maschinenzustands – Erkennen von Verschleiß oder Schäden an Bauteilen zur vorbeugenden Instandhaltung.
- Sicherstellung der Reproduzierbarkeit – Gewährleistung gleichbleibender Qualität bei wiederholten Fertigungsprozessen.
- Einhaltung von Normen und Vorschriften – Sicherstellung, dass die Maschine den Anforderungen z. B. nach ISO 230 oder VDI/DGQ 3441 entspricht.
Solche Vermessungen werden mit hochpräzisen Messgeräten wie Laserinterferometern, Messuhren oder 3D-Messsystemen durchgeführt.
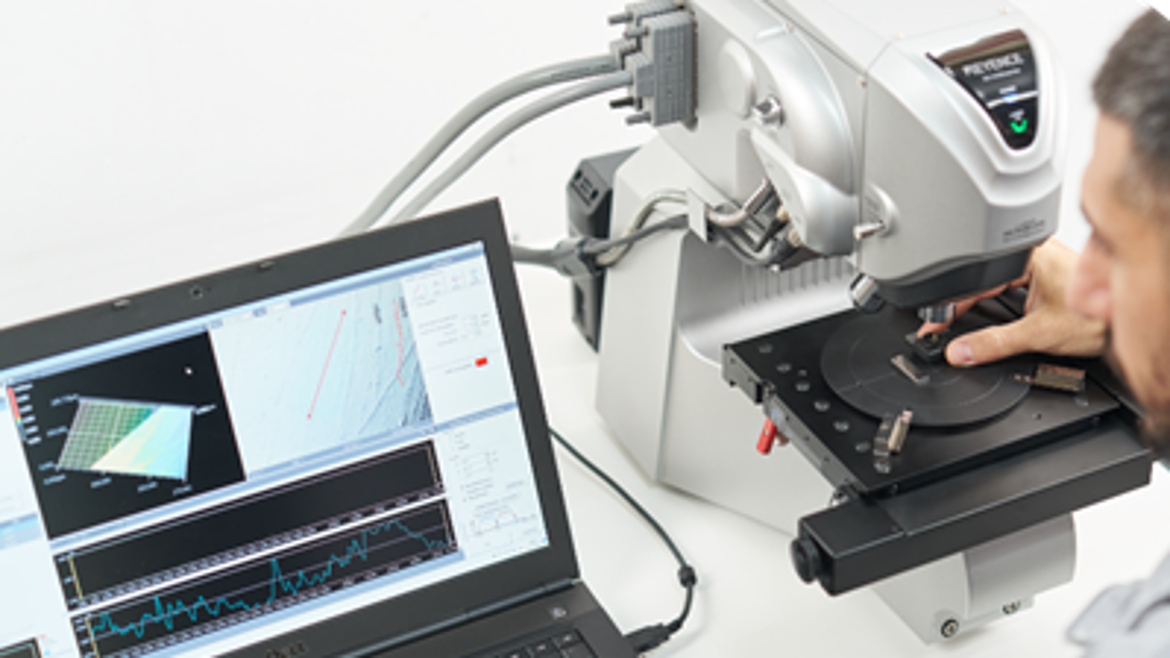
Oberflächenmessungen werden durchgeführt, um die Oberflächenbeschaffenheit eines Werkstücks zu analysieren und sicherzustellen, dass es die geforderten Qualitätsanforderungen erfüllt. Die Hauptziele sind:
- Funktionalität und Verschleißverhalten – Die Rauheit beeinflusst die Reibung, den Verschleiß und die Lebensdauer von Bauteilen, insbesondere bei Gleit- und Lagerflächen
- Qualitätskontrolle – Sicherstellung, dass gefertigte Teile innerhalb der vorgegebenen Toleranzen liegen und den technischen Anforderungen entsprechen
- Optimierung von Produktionsprozessen – Identifikation und Verbesserung von Bearbeitungsmethoden, um gewünschte Oberflächeneigenschaften zu erzielen
- Verbesserung der Haftung – Oberflächenrauheit beeinflusst die Haftung von Lacken, Beschichtungen oder Klebstoffen
- Reduzierung von Reibung und Geräuschentwicklung – In Anwendungen wie Motoren oder Getrieben ist eine optimierte Rauheit entscheidend für Effizienz und Geräuschminderung
- Einhaltung von Normen und Standards – Sicherstellung, dass die Oberflächenqualität den Anforderungen nach ISO 4287, ISO 25178 oder anderen relevanten Normen entspricht
Die Oberflächenmessungen erfolgt mit taktilen (z. B. Tastschnittverfahren) oder optischen Messverfahren (z. B. Laserscanningverfahren).
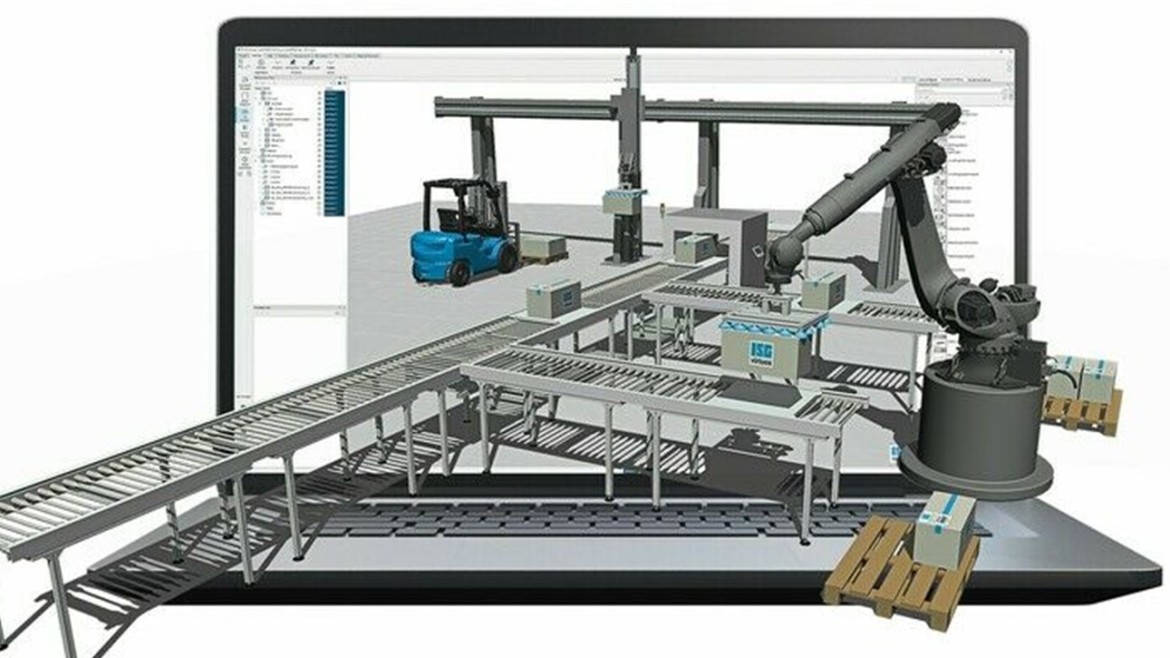
Eine Virtuelle Inbetriebnahme (VIBN) wird durchgeführt, um Maschinen, Anlagen oder Automatisierungssysteme bereits vor der physischen Inbetriebnahme in einer digitalen Umgebung zu testen und zu optimieren. Die Hauptziele sind:
- Fehlererkennung und Risikominimierung – Identifikation und Behebung von Steuerungs- oder Konstruktionsfehlern, bevor teure reale Tests notwendig sind. Vermeidung von unerwarteten Problemen beim Hochfahren der realen Anlage.
- Reduzierung von Kosten und Zeitaufwand – Verkürzung der realen Inbetriebnahmezeit durch frühzeitige Tests. Einsparung von Material- und Produktionskosten, da keine physischen Prototypen benötigt werden.
- Optimierung von Steuerungs- und Regelstrategien – Validierung von SPS-Programmen, HMI-Schnittstellen und Automatisierungsprozessen. Feinabstimmung der Maschinenparameter zur Effizienzsteigerung.
- Schulung von Mitarbeitern – Bediener und Wartungspersonal können bereits vor der physischen Inbetriebnahme geschult werden. Erhöhung der Sicherheit durch gefahrlose Simulation kritischer Szenarien
- Verbesserung der Produktqualität – Sicherstellung, dass das System wie geplant arbeitet und alle Qualitätsanforderungen erfüllt. Simulation verschiedener Betriebsbedingungen zur Optimierung der Leistung.
- Erleichterung der Integration in bestehende Systeme – Test der Kommunikation zwischen Maschinen, Steuerungen und IT-Systemen. Sicherstellung der Kompatibilität mit vorhandenen Produktionslinien.
Insgesamt ermöglicht die virtuelle Inbetriebnahme eine effizientere, sicherere und kostengünstigere Einführung neuer Maschinen und Produktionsprozesse.
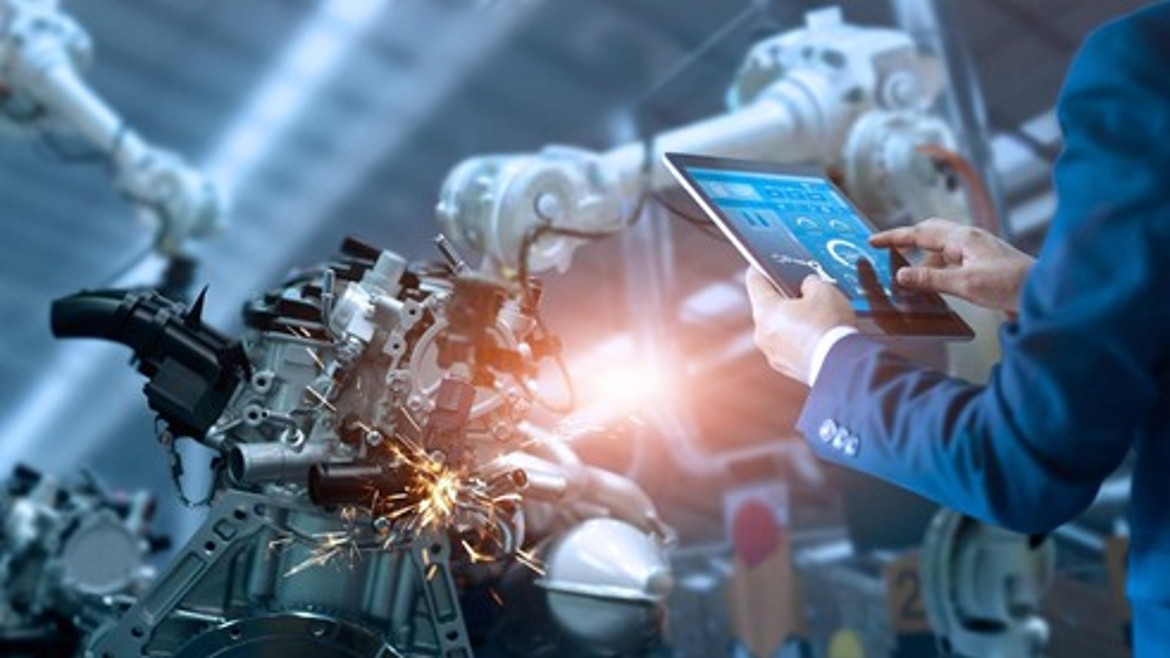
Industrial IoT (IIoT) steht für das "Industrial Internet of Things" und bezeichnet die Vernetzung von Maschinen, Sensoren und Systemen in industriellen Umgebungen. Durch die Nutzung von IoT-Technologien werden Produktionsprozesse intelligenter, effizienter und automatisierter.
Hauptmerkmale des IIoT:
- Vernetzte Maschinen & Sensoren – Maschinen und Anlagen kommunizieren über das Internet oder interne Netzwerke.
- Echtzeit-Datenverarbeitung – Sensordaten werden gesammelt, analysiert und zur Optimierung von Prozessen genutzt.
- Cloud- und Edge-Computing – Daten werden in der Cloud gespeichert oder direkt an der Maschine verarbeitet (Edge Computing).
- Automatisierung & Künstliche Intelligenz (KI) – KI-gestützte Analysen ermöglichen vorausschauende Wartung und Prozessoptimierung.
Anwendungsbereiche des IIoT:
- Predictive Maintenance (Vorausschauende Wartung) – Maschinen melden frühzeitig mögliche Ausfälle.
- Predictive Quality (Prognose der Bauteilqualität) – Mittels Sensordaten werden Vorhersagen zur erzielbaren Bauteilqualität generiert.
- Smart Manufacturing – Intelligente Fertigung durch Echtzeitüberwachung und -steuerung.
- Supply Chain Optimierung – Echtzeit-Tracking von Warenströmen und Lagerbeständen.
- Energie- und Ressourcenmanagement – Reduktion von Energieverbrauch und Emissionen durch intelligente Steuerung.
Vorteile des IIoT-Ansatzes:
- Höhere Effizienz durch Automatisierung und optimierte Prozesse.
- Geringere Ausfallzeiten dank vorausschauender Wartung.
- Verbesserte Produktqualität durch präzise Überwachung.
- Mehr Flexibilität und Anpassungsfähigkeit in der Produktion.
Typische IIoT-Technologien:
- Sensoren & Aktoren (z. B. Temperatur-, Druck-, Vibrationssensoren)
- Industrieprotokolle (z. B. OPC UA, MQTT)
- Big Data & KI zur Mustererkennung und Entscheidungsunterstützung
- 5G & Edge Computing für schnelle und dezentrale Datenverarbeitung
Beispiel: In einer Smart Factory erkennt eine mit IIoT vernetzte Maschine Verschleißerscheinungen anhand von Sensordaten. Das System meldet automatisch eine Wartung, bevor es zu einem Ausfall kommt. So bleiben Produktionsprozesse stabil und effizient.
IIoT ist die Grundlage für Industrie 4.0 und die digitale Transformation der Produktion.
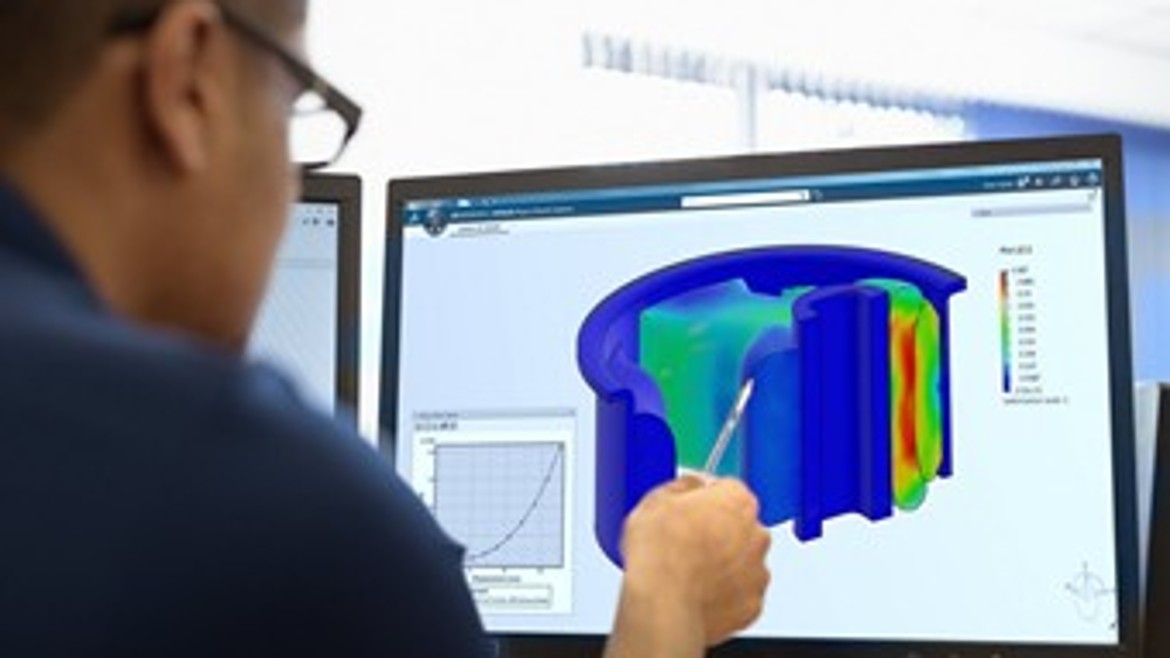
Eine FEM (Finite-Elemente-Methode) wird durchgeführt, um das mechanische Verhalten von Bauteilen und Strukturen unter verschiedenen Belastungen zu simulieren und zu analysieren. Sie ist ein wesentliches Werkzeug im Ingenieurwesen zur Optimierung von Konstruktionen und zur Reduzierung von Entwicklungszeiten.
Ziele der FEM:
- Strukturanalyse – Untersuchung von Spannungen, Dehnungen und Verformungen in Bauteilen.
- Optimierung der Konstruktion – Identifikation von Schwachstellen und Verbesserung der Materialnutzung.
- Reduzierung physischer Prototypen – Kosten- und Zeitersparnis durch virtuelle Tests statt aufwendiger Experimente.
- Nachweis der Belastbarkeit – Sicherstellung, dass ein Bauteil den realen Betriebsbedingungen standhält.
- Thermische Analyse – Untersuchung der Wärmeleitung, Erwärmung oder Kühlung von Bauteilen.
- Strömungsmechanik (CFD) – Simulation von Flüssigkeits- oder Gasströmungen, z. B. in Rohren oder Luftkanälen.
- Schwingungsanalyse – Prüfung auf Resonanz, Eigenfrequenzen oder Ermüdungserscheinungen.
Beispiel: Ein Ingenieur entwirft eine neue Autofelge. Mithilfe der FEM kann er simulieren, wie sich die Felge unter Fahrbelastung, Bremskräften und Stößen verhält. So kann er Schwachstellen erkennen und das Design optimieren, bevor ein physischer Prototyp gebaut wird.
Die FEM ist ein unverzichtbares Werkzeug zur Analyse und Optimierung von Bauteilen, wodurch Entwicklungszeiten verkürzt, Kosten gesenkt und Sicherheitsstandards verbessert werden.
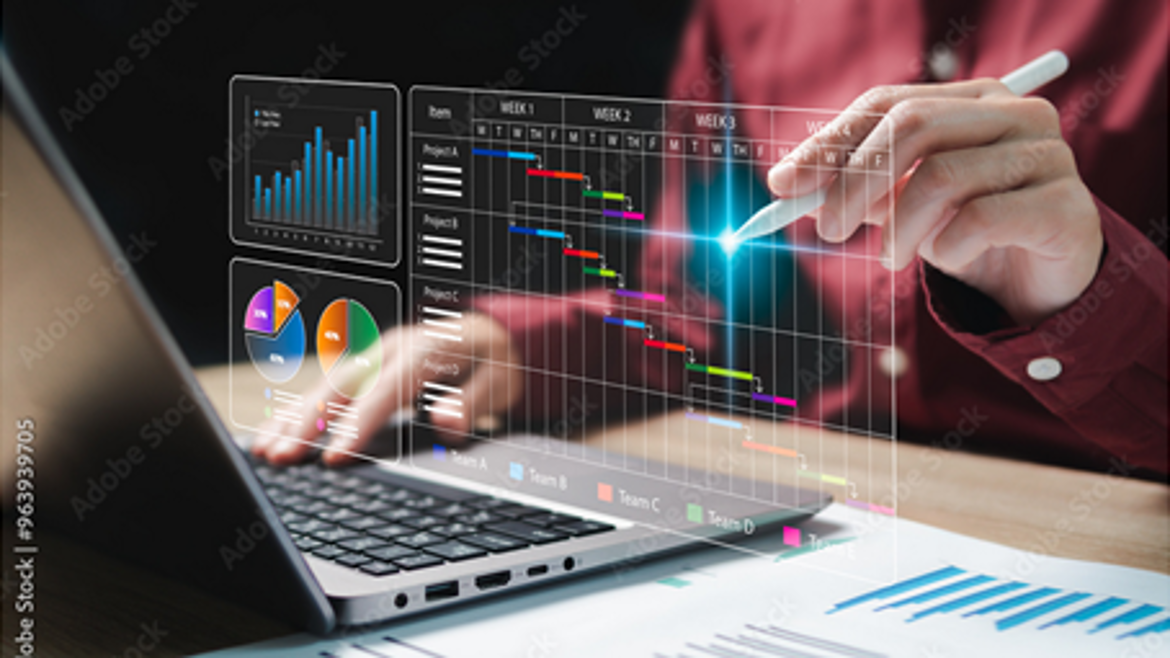
Produktionsplanung
Die Produktionsplanung legt im Voraus fest, was, wann, wie und womit produziert wird. Sie umfasst:
- Absatz- und Produktionsprogrammplanung – Festlegung, welche Produkte in welchen Mengen hergestellt werden sollen. Berücksichtigung von Kundenaufträgen, Marktanalysen und Lagerbeständen.
- Mengenplanung – Ermittlung des Materialbedarfs (Rohstoffe, Bauteile, Halbfertigprodukte). Einsatz von Materialbedarfsplanung (MRP = Material Requirements Planning).
- Termin- und Kapazitätsplanung – Erstellung von Produktionszeitplänen mit exakten Start- und Endterminen. Berücksichtigung von Maschinenkapazitäten, Personalverfügbarkeit und Schichtplänen.
- Arbeitsplanung – Definition der benötigten Arbeitsgänge und Arbeitsmittel. Optimierung der Reihenfolge von Bearbeitungsschritten zur Verkürzung der Durchlaufzeiten.
Produktionssteuerung
Die Produktionssteuerung sorgt dafür, dass die geplanten Aufträge tatsächlich umgesetzt werden. Sie umfasst:
- Auftragsfreigabe – Entscheidung, wann ein Auftrag gestartet wird. Bereitstellung aller notwendigen Materialien, Werkzeuge und Kapazitäten.
- Produktionsüberwachung – Laufende Kontrolle des Produktionsprozesses (z. B. Maschinenlaufzeiten, Qualitätsprüfungen). Reaktion auf Störungen (Maschinenausfälle, Lieferverzögerungen, Qualitätsprobleme).
- Anpassung und Nachsteuerung – Eingreifen bei Planabweichungen (z. B. neue Priorisierung von Aufträgen). Optimierung von Ressourcennutzung (z. B. Maschinenverlagerung, Personalumplanung).
Ziele der Produktionsplanung und -steuerung
- Hohe Termintreue – Produkte werden pünktlich geliefert.
- Optimale Ressourcennutzung – Minimierung von Material- und Zeitverschwendung.
- Geringe Lagerbestände – Produktion nach Bedarf (z. B. Just-in-Time-Fertigung).
- Flexibilität – Reaktion auf Störungen oder Änderungen der Nachfrage.
- Kostenreduktion – Vermeidung von Engpässen, Überproduktion oder Leerlaufzeiten.
Beispiel: Ein Automobilhersteller nutzt PPS, um sicherzustellen, dass alle Karosserieteile, Motoren und Elektronikkomponenten zur richtigen Zeit und in der richtigen Menge an den Montagelinien bereitstehen.
Die Produktionsplanung und -steuerung sorgt dafür, dass Produktionsprozesse effizient, wirtschaftlich und reibungslos ablaufen – von der ersten Planung bis zur Fertigstellung des Produkts.
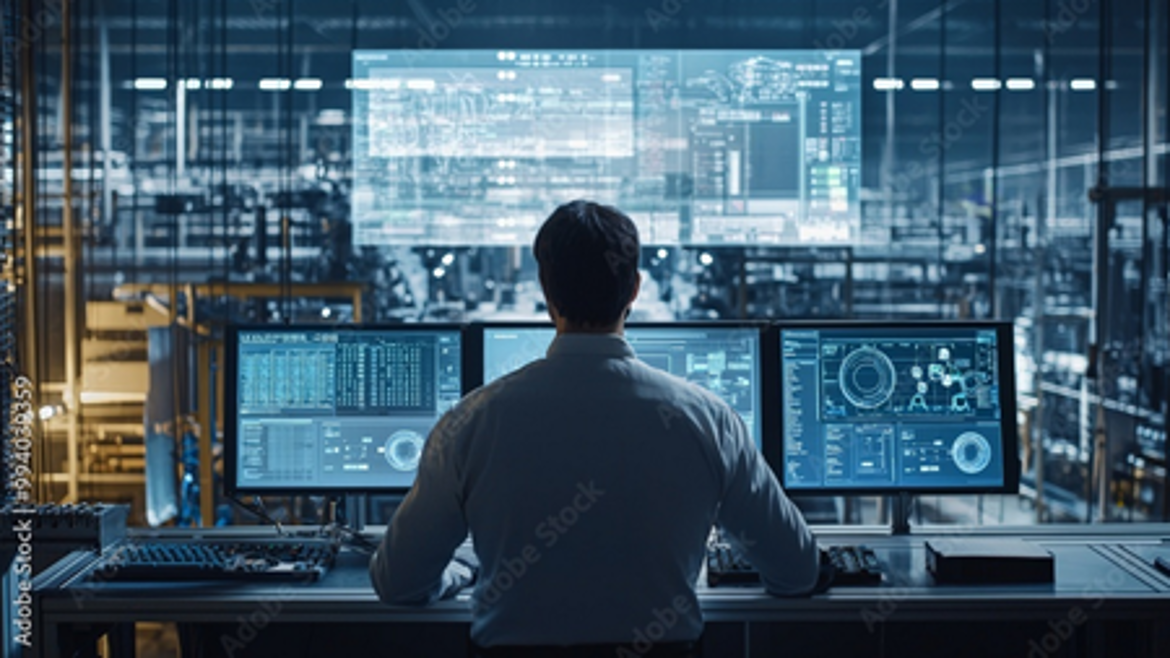
Eine Produktionsprozessanalyse ist eine systematische Untersuchung und Bewertung eines Produktionsprozesses mit dem Ziel, Effizienz, Qualität und Wirtschaftlichkeit zu optimieren. Dabei werden alle Schritte des Fertigungsprozesses analysiert, um Schwachstellen zu identifizieren und Verbesserungspotenziale aufzudecken.
Ziele der Produktionsprozessanalyse
- Erhöhung der Effizienz – Identifikation und Beseitigung von Engpässen und unnötigen Prozessschritten.
- Reduzierung von Kosten – Einsparung von Material, Energie und Arbeitsaufwand.
- Verbesserung der Produktqualität – Minimierung von Fehlern, Ausschuss und Nacharbeit.
- Verkürzung der Durchlaufzeiten – Optimierung der Produktionsgeschwindigkeit.
- Erhöhung der Flexibilität – Anpassung an veränderte Kundenanforderungen oder Marktbedingungen.
Methoden der Fertigungsprozessanalyse
- Wertstromanalyse (VSM – Value Stream Mapping) – Darstellung des gesamten Material- und Informationsflusses einer Produktion. Identifikation von Verschwendungen (z. B. Wartezeiten, unnötige Transporte). Grundlage für Lean Production-Optimierungen.
- Zeit- und Bewegungsstudien – Untersuchung von Arbeitsabläufen mit Methoden wie REFA oder MTM (Methods-Time Measurement). Reduzierung unnötiger Handgriffe zur Produktivitätssteigerung.
- Ursachenanalyse (Ishikawa-Diagramm, 5-Why-Methode) – Identifikation der Hauptursachen für Qualitätsprobleme oder Produktionsfehler. Systematische Problemlösung durch tiefgehende Analyse.
- OEE-Analyse (Overall Equipment Effectiveness) – Messung der Gesamtanlageneffektivität anhand von Verfügbarkeit, Leistung und Qualität. Aufdeckung von Produktionsverlusten (z. B. ungeplante Stillstände, langsame Zyklen, Ausschuss).
- FMEA (Fehlermöglichkeits- und Einflussanalyse) – Bewertung potenzieller Fehlerquellen im Fertigungsprozess. Vorbeugende Maßnahmen zur Risikominimierung.
Beispiel: Ein Unternehmen stellt Metallgehäuse für Maschinen her. Durch eine Wertstromanalyse stellt sich heraus, dass Bauteile oft in Zwischenlagern warten, bevor sie weiterverarbeitet werden. Durch eine Umstellung auf einen One-Piece-Flow-Ansatz wird die Durchlaufzeit um 30 % verkürzt.
Die Fertigungsprozessanalyse ist ein wesentliches Werkzeug, um Produktionsabläufe kontinuierlich zu verbessern. Sie hilft Unternehmen, ihre Fertigung effizienter, kostengünstiger und qualitativ hochwertiger zu gestalten.